Introduction to Wooden Base Packing
Wooden base packing represents a vital component within various industrial supply chains, offering resilient support for goods during transportation and storage. This method of packing utilizes wooden materials as a structural base, providing a range of benefits that enhance product integrity and safety. The significance of wooden base packing can be seen across numerous industries, including manufacturing, logistics, and pharms, where the protection of goods is paramount.
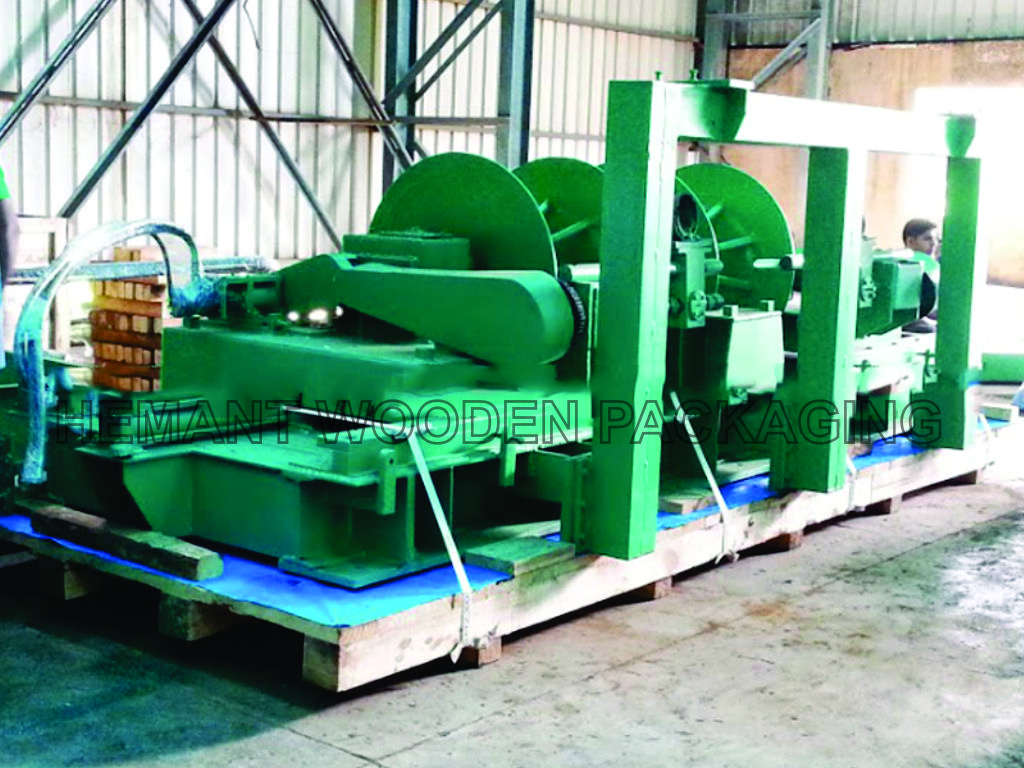
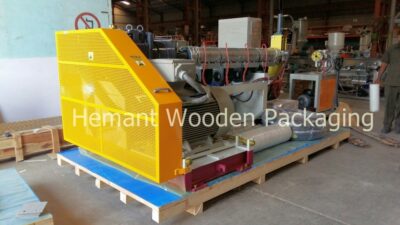
One of the primary reasons for the preference of wooden bases in packing is their remarkable durability. Unlike other materials, wood possesses natural strength that can withstand significant weights and pressures, making it an ideal choice for heavy machinery or fragile items. Furthermore, wooden base packing is less prone to breakage during transit, reducing the risk of product damage and related financial losses.
In addition to their strength, wooden bases are known for their versatility. They can be customized in dimensions and designs to accommodate specific types of products, thereby maximizing the efficiency of the packing process. This adaptability is crucial in industries where different item shapes and sizes are commonplace.
Moreover, wooden bases demonstrate excellent environmental resilience. They can endure various climatic conditions, including humidity and temperature fluctuations, ensuring the stability of the packed items regardless of external influences. This characteristic makes wooden base packing particularly advantageous for long-haul transportation where products might be exposed to less than favorable environments.
Overall, the integration of wooden base packing into industrial applications reflects an enduring preference for a material that offers strength and reliability. By understanding the significance and advantages of wooden base packing, businesses can make informed decisions to better protect their assets while enhancing logistical efficiency.
Types of Wooden Base Packing Materials
When it comes to wooden base packing for industrial use, the choice of material is crucial. Each type of wood offers distinct properties that can impact the durability, strength, and cost-effectiveness of packing solutions. The three primary types of materials commonly used are plywood, hardwood, and pine wood products.
Plywood is a popular choice due to its versatility and strength. Composed of multiple layers of wood veneer glued together, plywood exhibits exceptional resistance to warping and splitting. This layered construction provides added stability, making it suitable for various industrial applications where heavy loads may be involved. Furthermore, plywood can be produced in different grades and thicknesses, catering to the specific needs of businesses looking for customized solutions.
Hardwood is another option that boasts durability and visual appeal. Types of hardwood such as oak, maple, and cherry are often chosen for their robustness and ability to withstand harsh conditions. Hardwood’s density contributes to its strength, making it ideal for situations that require a solid packing base. Additionally, the natural beauty of hardwood can enhance the aesthetic value of packaged products, although this may come at a higher cost compared to other materials.
Lastly, pine wood products, Pine wood products are often lighter and more economical than solid wood, making them an appealing choice for cost-conscious businesses.
In summary, selecting the appropriate wooden base packing material is essential for ensuring product safety and integrity during transportation and storage. Each option—plywood, hardwood, and pine wood—offers unique advantages that can be beneficial in various industrial contexts.
Benefits of Using Wooden Base Packing
Wooden base packing is a widely recognized option in the realm of industrial logistics, offering numerous advantages that enhance the efficiency and safety of transporting goods. One of the primary benefits of wooden base packing is its exceptional strength-to-weight ratio. This characteristic allows manufacturers and distributors to use a material that is both robust and lightweight, minimizing the weight added to the overall shipment while ensuring that the products are securely cradled during transit. Such a balance is crucial in optimizing shipping costs and maintaining the integrity of the packed items.
Additionally, wooden packing is celebrated for its recyclability, making it an environmentally responsible choice for businesses aiming to reduce their carbon footprint. Unlike many synthetic materials, wood can be repurposed or recycled at the end of its lifecycle, thus contributing to sustainable practices. Companies consciously using wooden base packing can enhance their eco-friendliness, which increasingly influences purchasing decisions among environmentally conscious consumers.
Cost-effectiveness is another significant advantage associated with wooden base packing. The availability and affordability of raw materials allow businesses to source wooden pallets and crates at a lower cost compared to other packing alternatives. Consequently, organizations can enjoy substantial savings in their logistics operations. Moreover, the durability of wooden packing minimizes the risk of damage during transportation, promoting product safety and reducing the costs associated with returns or replacements.
Incorporating wooden base packing within supply chains also fosters improved logistics. Its adaptability to various product sizes and weights ensures seamless integration into existing logistics frameworks, leading to more efficient storage and handling practices. By leveraging the benefits of wooden base packing, industries can enhance operational efficiencies, safeguard products, and support sustainable growth. This multifaceted approach ultimately positions wooden base packing as a vital component in modern industry logistics.
Standards and Regulations for Wooden Packing
Wooden packing materials are integral to various industries, especially when it comes to the shipping and storage of goods. However, the unregulated use of wooden packing can lead to significant problems, including the spread of pests and diseases. Therefore, adhering to international and regional standards and regulations is essential for global trade. One of the most critical guidelines is the International Standards for Phytosanitary Measures No. 15 (ISPM 15). This regulation specifically addresses the treatment of wood packaging material (WPM) and aims to prevent the spread of harmful organisms across borders.
ISPM 15 mandates that wooden packing materials be treated through approved methods, such as heat treatment or fumigation, to eliminate any potential infestations. Additionally, compliance with ISPM 15 requires that all treated wooden packing be marked appropriately to signify that it meets international standards. This certification process not only ensures that the wooden materials are safe for transport but also protects businesses and supply chains from potential economic losses related to pest control and exports.
Many countries have adopted ISPM 15 along with their local regulations, making it imperative for businesses to remain informed about the specific requirements within their operating regions. For instance, in the United States, the Animal and Plant Health Inspection Service (APHIS) enforces these standards, while the European Union has also established its own set of regulations governing wooden packaging. Understanding these regulations is crucial; non-compliance can lead to severe repercussions, including fines and the rejection of shipments. Thus, businesses should implement proper practices to ensure compliance with wooden packing standards to facilitate smooth and efficient international shipping processes.
Applications of Wooden Base Packing in Various Industries
Wooden base packing plays a pivotal role in various industries, offering robust support and protection for goods during transportation and storage. Manufacturing is one of the key sectors where wooden base packing is indispensable. In this industry, heavy machinery parts and equipment require stable and reliable packing solutions to prevent damage. For instance, a leading manufacturing company utilized wooden crates to ship complex machinery overseas, effectively safeguarding sensitive components against the rigors of transportation.
Similarly, the construction industry benefits significantly from wooden base packing. Large construction materials, such as beams, tiles, and pre-cast concrete elements, necessitate sturdy packaging to avert breakage during transit. A notable case involved a construction firm that adopted wooden pallets to transport structural steel components. The inherent strength of the wooden base packing ensured that the materials arrived on-site without any noticeable damage, reducing costs associated with replacements and delays.
The electronics industry also sees a growing application of wooden base packing. Delicate electronic devices require careful handling to avoid damage. A leading electronics manufacturer started using custom-designed wooden boxes to protect their products during shipment. The unique properties of the wooden base packing minimized vibration and shock, ensuring that sensitive components reached retailers in optimal condition.
Overall, wooden base packing demonstrates versatility across these industries, providing effective solutions tailored to meet diverse packing needs. Its reliability and strength underline its importance in facilitating smooth operations in complex logistics frameworks.
Sustainability and Environmental Impact of Wooden Packing Materials
Wooden base packing materials have gained significant attention in recent years due to their sustainability and environmental benefits compared to traditional packing options. One of the primary advantages of using wooden materials lies in their ability to be sourced from sustainably managed forests. Responsible forestry practices ensure that trees are replanted and harvested in a manner that does not deplete resources, allowing forests to thrive while supporting biodiversity. This ethos promotes an ecological balance essential for maintaining healthy ecosystems.
Moreover, wooden packing materials offer excellent reusability options, which enhances their sustainability profile. Unlike single-use packing materials, wooden bases can be employed multiple times, thereby reducing waste generation. Many businesses are exploring creative ways to implement container reuse systems, benefiting not only the environment but also the bottom line. By investing in long-lasting wooden options, companies can minimize reliance on non-biodegradable materials, aligning their operations with corporate social responsibility initiatives.
Biodegradability is another key aspect that underscores the environmental advantages of wooden packing solutions. Wooden materials decompose over time, reverting back to the earth without leaving harmful residues. In contrast, plastic and polystyrene materials can persist for decades, contributing to landfill overcapacity and pollutant accumulation. Utilizing wooden base packing not only helps reduce waste but also provides a circular economy approach where materials can return to nature and foster soil health.
In sum, the shift towards wooden packing materials represents a significant step businesses can take to enhance their sustainability efforts. By prioritizing responsible sourcing, improving reusability, and leveraging the natural biodegradability of wood, organizations can minimize their environmental footprint and contribute positively to the planet. This conscientious approach serves not only the business objectives but also promotes a healthier, more sustainable future.
Best Practices for Handling and Storing Wooden Base Packing
Proper handling and storage of wooden base packing are essential for maintaining its integrity and ensuring its performance in various industrial applications. One of the primary best practices involves inspecting the wooden packing materials upon receipt. Look for signs of damage, moisture, or pest infestation, as these factors can compromise the quality and durability of the packing.
When handling wooden base packing, it is critical to use appropriate equipment, such as forklifts and pallet jacks, to prevent any accidental damage. Manual handling should be minimized, but when necessary, proper lifting techniques should be employed to avoid injuries and potential damage to the packing. To further safeguard wooden materials, avoid stacking heavy items on top of them. Instead, store them in a designated area that is protected from excessive weight, moisture, and temperature fluctuations.
Storage conditions play a crucial role in preserving wooden base packing. Ideally, wooden packing should be kept in a climate-controlled environment where humidity levels are maintained between 30% and 50%. High humidity can lead to warping, mold growth, and decay, while excessively dry conditions can cause cracking and splitting. To enhance protection, consider utilizing breathable covers or tarps, which allow for air circulation while shielding the wood from external elements. Additionally, wooden base packing should be stored off the ground on pallets or shelves to prevent contact with moisture and pests.
Finally, when preparing wooden base packing for transportation, ensure that each unit is properly secured to prevent shifting or damage during transit. Utilizing straps and shrink wrap can help maintain stability and protect the packing from environmental factors. By implementing these best practices for handling and storing wooden base packing, industries can significantly reduce damage, extend the life of the materials, and ultimately enhance operational efficiency.
Conclusion: The Future of Wooden Base Packing in Industry
In recent years, wooden base packing has become a crucial component in the industrial sector. This trend is shaped by various factors, including the increasing focus on sustainability, the advancement of packing technology, and the evolving standards set by regulatory bodies. As industries continue to grow, the demand for efficient and environmentally friendly packing solutions becomes more pressing.
Sustainability is one of the most prominent trends influencing the future of wooden base packing. As manufacturers seek to minimize their environmental impact, the utilization of renewable materials like wood aligns well with these objectives. Unlike plastic or metal, which poses recycling challenges, wooden packing components can be sourced sustainably and are biodegradable. This shift is not merely a market trend but a necessity, driven by consumer preferences and regulatory pressures to adopt greener practices.
Additionally, technological advancements are revolutionizing the design and functionality of wooden base packing. Innovations in manufacturing processes, such as precision cutting and automated assembly, allow for more complex designs that enhance stability and protection during transportation. These developments can lead to better optimization of space and weight, ultimately reducing shipping costs and improving efficiencies across the supply chain.
Furthermore, the industry is witnessing evolving standards and regulations aimed at improving safety and performance. As companies prioritize compliance, they will likely invest in improved wooden packing solutions that meet rigorous specifications. Collaborations between materials scientists and engineers are expected to yield composite materials that offer even greater strength and durability while still being sustainable.
Overall, the future of wooden base packing in the industrial sector appears promising. With the continuous push toward sustainability, technological advancements, and stringent industry standards, wooden base packing is set to play an increasingly pivotal role in shaping modern industrial practices. These trends indicate not only a transformation in how goods are packed and shipped but also a broader commitment to environmental stewardship and operational excellence.